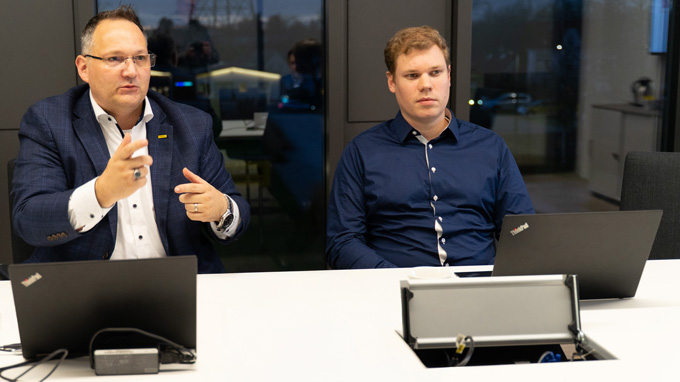
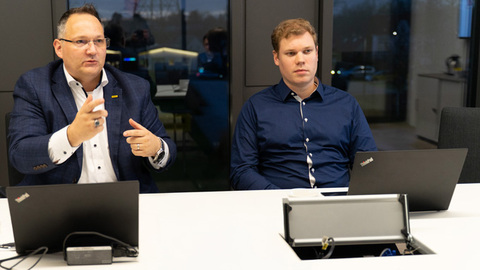
Decentralized Control Technology for Modular and Scalable Conveyor Lines
Turck’s compact TBEN I/O modules from its TBEN series not only enable the control of drum motors on roller tracks but also the digitalization of the entire conveying line, while at the same time ensuring transparency in intralogistics. Michael Corban, editor-in-chief of the German trade journal KEM, interviewed the four Turck specialists Frank Morassi, Holger Spies, Frederik Nitsche and Hendrik Schnabel to find out how decentralized automation, modularization and digitalization make it possible to implement flexibly scalable and highly available conveying lines – a particularly efficient approach when combined with RFID technology for conveyed goods identification.
What are the challenges that Turck is meeting with this intralogistics offering?
Frank Morassi (Vertical Sales Manager Intralogistics): In intralogistics, no two systems are the same – flexibility is key. Not only with regard to the components used, but also in order to redesign the conveyor system quickly to meet today’s frequently and rapidly changing requirements. On the mechanical engineering side, the answer is modularization; in automation, it is decentralized automation in conjunction with digitalization – and this is where we are at home. In this way we can implement modular and flexibly scalable conveyor lines – offering a high level of availability and operation with zero pressure accumulation if required. With this approach, we can solve a number of tasks that will increasingly arise in the coming years.
If requirements change, scalability is needed in addition to the rapid redesign of a system. Modular design and decentralized automation enable conveyor modules to be adapted and expanded quickly and easily to suit a new line layout. With smart and robust I/O modules on board, the wiring effort stays negligible – the modules also come with control capabilities and connections for actuators and sensors, including a 24 or 48-volt power supply. Since we have always based our product ranges on modular and holistic concepts, Turck can offer intralogistics specialists a single source solution – and bring together decentralized automation, traceability, condition monitoring, scalability, a fast time-to-market and digital services with our Turck Automation Suite. Our RFID expertise should also be mentioned here.
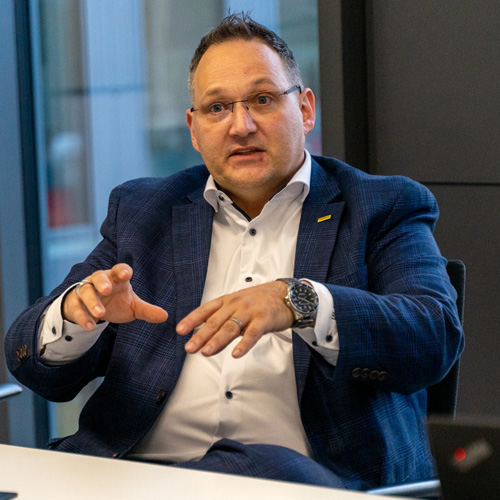
Could you expand on this?
Morassi: With the multitude of tasks involved – for example, when something is assembled, welded, soldered, packed, stored, temporarily stored, relocated or repacked – it is important to record exactly which box or assembly is currently where. We can record this very well using RFID – and not just via gates at the incoming and outgoing goods areas. We can initiate entries and withdrawals in the higher-level system at the respective stations. Unlike barcodes, an enormously important advantage of RFID is the ability to not only read the tag but also to write to it. For example, the serial numbers of the installed parts and assemblies can be easily provided during assembly processes – traceability is guaranteed.
You also mentioned the topic of a fast time-to-market...
Morassi: ...because that is one of the advantages of decentralized automation. We can implement a system more quickly because decentralized systems are run and tested autonomously. This makes it possible to implement a new system or even a system expansion more quickly. At the same time, we also have the opportunity to collect and process data very easily. This allows the creation of added value – for example for service tasks, not least through data analysis in the cloud.
This is where our automation software, the Turck Automation Suite (TAS), comes into play. This tool enables us to easily incorporate and integrate all components. Ideally, each element of a conveyor line is provided with one of our I/O modules – so that data can be recorded and passed on to the higher-level control system.
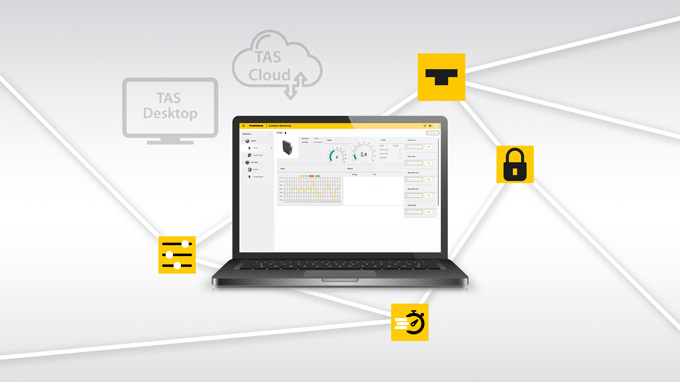
The smart I/O modules also have a controller – how do local and higher-level controllers interact?
Holger Spies (Project Manager Sales): By installing one of our TBEN modules ‘at every meter’ of the conveyor line, we not only enable full control of the roller motors in the particular conveyor module, but we can also address everything that can be controlled locally – i.e. decentrally – via the integrated controller. I would like to emphasize that we can even process tasks with real-time requirements. The higher-level controller then does not have to perform any detailed tasks on the individual modules and only orchestrates the overall system. Besides the control tasks of the modules, data is also collected and forwarded for predictive maintenance.
Let me briefly illustrate this with an example: Supposing a package is to be ejected at station X. We then record the information locally and pass it on via our module. In other words, we identify the package and control the related ejection unit via the decentralized automation locally. This also applies if it is a real-time application. In this case, no information needs to pass through the central controller. For example, this enables the motor rollers to be controlled locally according to the respective task. The CAN-based communication protocol also allows us to transmit additional data at the same time and run specific profiles, or conversely, read out values for temperature, current and voltage. The aim is to achieve digital consistency and thus eliminate the limitations of the usual analog interfaces. Digitalization gives us the opportunity to maintain transparency about the state of the entire system – right down to the last meter.
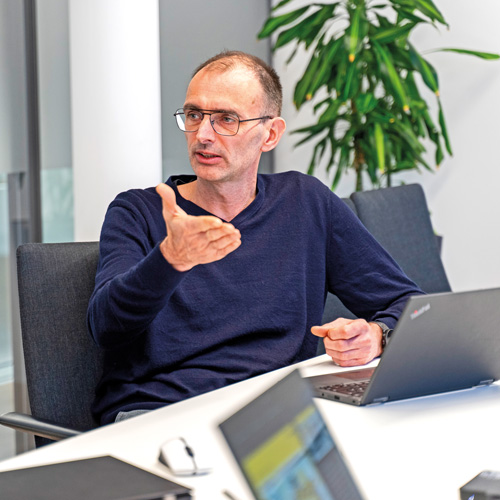
Does this then enable condition monitoring?
Spies: Exactly! This is because we can now determine the required current broken down for each individual motor roller, thus not only opening up the possibility of further control options but also laying the foundation for predictive maintenance. Only with this data transparency can system builders offer their customers, for example, the ability to replace specific motor rollers in advance – such as if they start to draw higher currents after a defined number of operating hours.
In summary, decentralized automation enables us to also process real-time applications locally in the field and thus offer total flexibility, from the control and scaling of conveyor lines right through to solutions for predictive maintenance.
What are the other features of the smart I/O modules used?
Frederik Nitsche (Product Manager Factory Automation Systems): We always build our IP67 modules for suitability in severe environmental conditions – vibration resistance is particularly important in intralogistics. In addition, we also allow a 48-volt power supply for the motor – this sounds trivial, but effectively halves the currents, which is particularly important in extensive intralogistics systems. Each Turck module can supply and control four roller motors – and thus a complete conveyor module.
As already mentioned, we are of course not just limited to the roller motors in terms of control tasks but can also perform other tasks. All in all, this provides intralogistics specialists with an easy and flexible decentralized logic system that works very efficiently on the conveyor modules and also enables zero pressure accumulation conveying. This is a wonderful way to automate segments of roller conveyor systems.
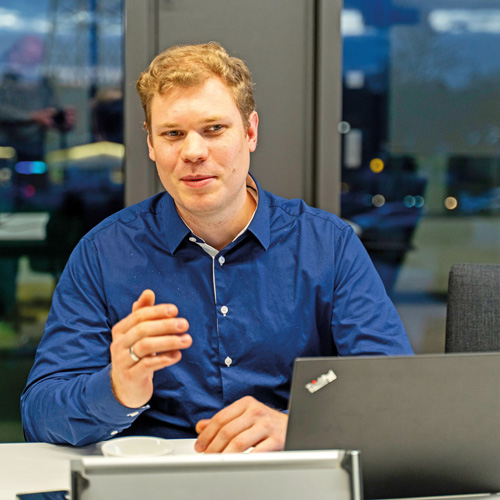
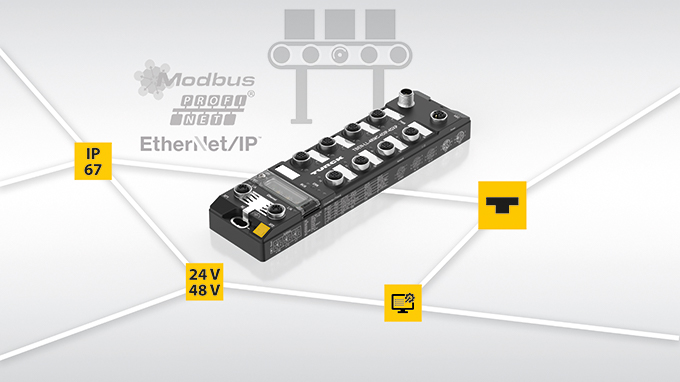
Am I dependent on specific manufacturers for the motor rollers?
Nitsche: We currently support CAN-based motors from MTA, MPC and Interroll. In line with the core idea of modularization, we incorporate both the actual logic and the digital roller connection. In this way, nobody has to worry about data mapping, and you can control the speed at any time via Profinet or EtherNet/IP or, conversely, read out data for predictive maintenance. Based on our TBEN-LL4RM-4DI-4DXP I/O module, for example, we have further developed a module for SSI SCHAEFER to create a “Conveyor Control Unit”. Digital inputs and outputs for external trigger signals or actuators were an additional requirement here, in addition to the 48-volt supply for the roller motors and 24 volts for conventional actuators, CAN communication to the motor and Profinet to the controller. Besides four conventional I/Os, four DXP ports are provided on the module, which can be used either as in- or outputs.
Spies: As already mentioned, these modules can also be used to solve real-time control tasks, especially in conjunction with Turck’s RFID system – such as our new RFID tunnel. In intralogistics, I often have tasks such as checking whether there really are five tags in a box – if there are only four, I have to be able to eject the box directly and return it. The critical factor is always giving users the ability to decide whether they want to solve these kinds of tasks locally on the relevant module or centrally – we can do both. This is a tremendous benefit, particularly for expansions and conversions.
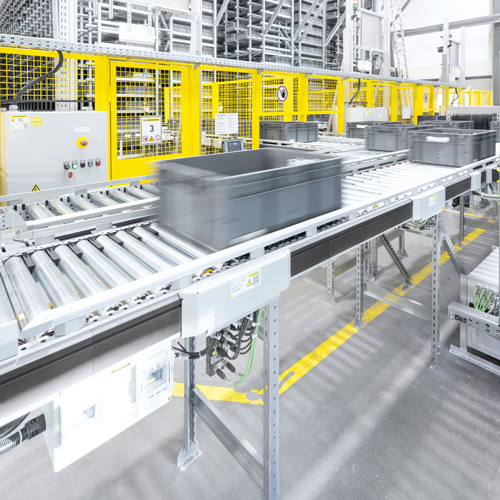
How easy is it to integrate this kind of RFID tunnel?
Hendrik Schnabel (Product Manager RFID UHF Systems): Very easy – and above all in a scalable way. Our RFID tunnel provides an RFID read point that can be very easily attached to the conveyor system. I emphasize this because the implementation of this kind of read point in surroundings of predominantly metal conveyor technology is not a straightforward task. To achieve reproducible read results, the read point must be well shielded and aligned with the conveyor belt. All this is already included in our RFID tunnel, thus offering the benefit that the user can easily add more tunnels when expanding the system – everything is already pre-assembled. RFID also plays an important role here because, with the high demands placed on identification in intralogistics, we are reaching a technological limit where the conventional barcode is no longer sufficient.
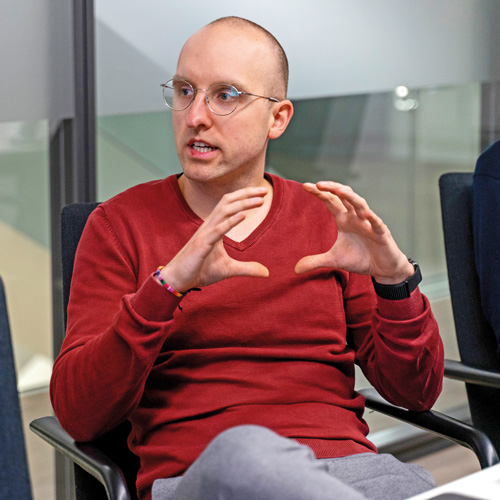
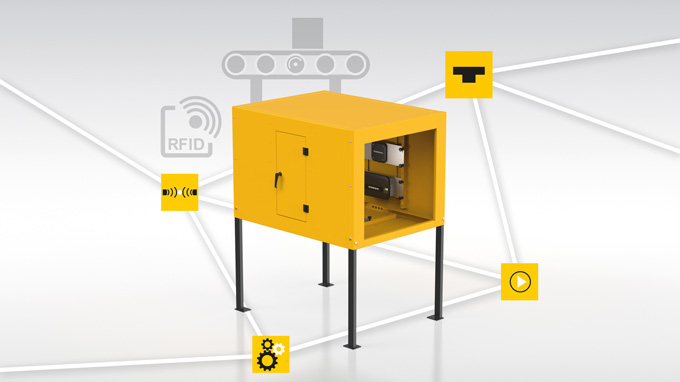
You have already mentioned the metal environment – has a solution been found for the reading of RFID tags on metal or liquids?
Schnabel: This is still fundamentally an issue – but a solution exists in the form of special metal tags, for example. For these kinds of requirements we also offer consulting services – because these cases are usually complex and require close examination. However, intralogistics today mainly involves the use of plastic containers and carriers so that the reading of tags is not a problem.
Author | Michael Corban is editor-in-chief of the trade journal KEM Konstruktion | Automation
Further Information
- Topics & Technologies