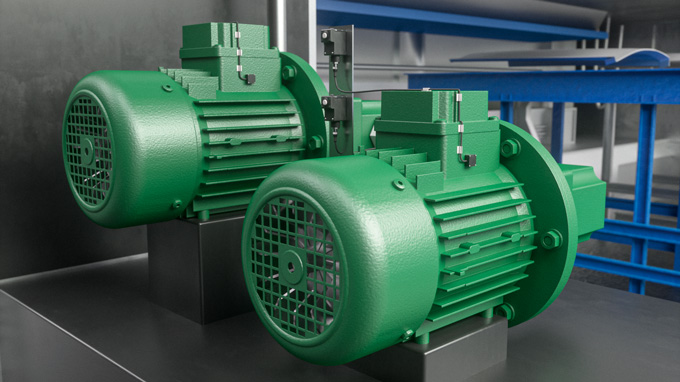
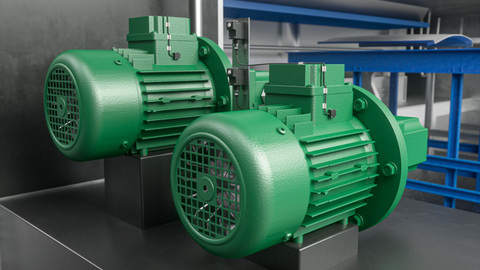
Efficient Data Transfer and Visualization in Existing Plants
Existing plants can be made fit for condition monitoring in no time at all using smart sensors and flexible solutions for data transfer and visualization
Quick Read
The lack of the necessary technical requirements and the ongoing production processes often impede the later introduction of a condition monitoring system in existing industrial plants. Turck offers easy to install sensors and suitable data transfer and monitoring solutions especially for these kinds of brownfield projects. Directly mounted on the motor, Banner Engineering's QM30 vibration and temperature sensor supplies for example measured values, which reach an HMI via a wired or wireless connection or can be sent with encryption via Turck's TCG20 cloud gateway to mobile terminals.
Building from scratch is often not always trouble-free but there is a clear benefit: Requirements can be taken into consideration early on in the new structures. This also applies to maintenance. Anyone planning a modern production plant or a logistics center can equip machines and plants with smart sensors in order to selectively query the status data of individual devices or areas at a later time. Performing inspections remotely and efficiently planning maintenance – thanks to fast fieldbus networks and industrial Ethernet.
What do you do, however, if the system architecture comes from a previous decade? This is normally the case in practice, with all the associated challenges for the technical personnel. When implementing smart condition monitoring in an existing plant, maintenance technicians face many obstacles: How should the retrofit be successfully completed without any intervention in ongoing processes? Does the control system have to be adapted? How do I access information on machines that are difficult to access?
Motor monitoring as a retrofit
This is where tailored stand-alone solutions come into play, from basic local monitoring tasks right through to wireless communication and the transfer to cloud environments. The idea: Companies can easily add at a later time devices by which they monitor machine values within an independent system. Status data can then always be transferred to the customer's automation world if required, with the existing architecture always however remaining separate to the operation of the condition monitoring expansion.
The monitoring of motors is a widely used application of this approach. These drive pumps, compressors or exhaust fans, and are often run in noisy uninterrupted duty in locations that have so far been difficult to reach for maintenance. A regular inspection by employees cannot exclude the possibility of an impending machine failure with a high degree of certainty; onsite inspections are also mostly difficult. Monitoring through the use of measurement devices is not only more reliable but also more economical. They can measure three different values: vibration, temperature and current.
IP67 sensor monitors vibration and temperature
Irregularities in a motor sometimes announce themselves several months before the actual failure. An incorrectly adjusted shaft, a sticking bearing or imbalance in an attachment will change the frequency in the vibration. To detect these, maintenance engineers can fit the QM30 vibration and temperature sensor directly to the motor block. The compact sensor with IP67 protection is fitted easily and securely with magnets. It is based on a microelectro-mechanical system (MEMS) and thus supplies high precision velocity and acceleration data in two dimensions. The QM30 also outputs a temperature value, and registers therefore in the temperature range from -40 to 105 °C, whether and where the motor has overheated, and thus allows the monitoring of temperature trends.
The current required by the motor is also helpful here. If there is any damage to bearings, or if the lubrication is not correct, the mechanical resistance will make more current necessary to reach the required speed. A measurement transformer can be used for monitoring.
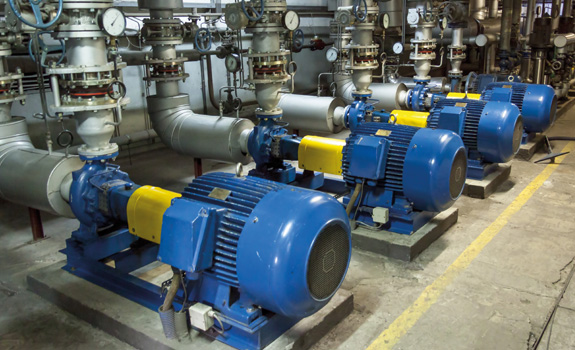
Data transfer in the wireless network
These measured values can be used in different ways and can be transferred in both wired and wireless networks. In some machine halls, a decentralized alarm system, for example, consisting of the QM30VT2 sensor and Turck's compact TBEN-S2-2COM I/O module are perhaps all that is needed to meet the requirements. Thanks to the integrated intelligence through the ARGEE programming environment, the fieldbus module takes over PLC functions if required and transfers the information of an overshot threshold value directly to a signal light. Alternatively, the TBEN module can also be connected with an HMI device.
Even more flexibility is provided by a wireless transfer within Banner's proprietary DX80 wireless system. For this a device like the QM30VT1 vibration and temperature sensor is connected serially with a transmission module (node) which sends the data to a receiver (gateway). In order to also determine changes in current consumption, users can use a special DX80 node which offers an additional input for the signals of a transducer. If required, the wireless nodes can be battery-driven so that no additional power supply has to be laid. This considerably reduces the required wiring effort. Added to this is the possibility to implement the monitoring precisely at the ideal location.
This may, for example be a central control room. The wireless gateway and Turck's TX700 HMI can be linked here to display the status data of several machines with the VisuPro software, to extract log files or to configure alarms. The data transfer does not have to end at the HMI since other destinations are made possible via an Ethernet connection: the Internet browser for visualization in WebVisu or for sending automatic email notifications, as well the in-house automation environment (PLC, HMI etc.).
Condition Monitoring: Most Important Systems Explained in Detail
From the cloud to the mobile terminal
Condition monitoring, however, is not restricted to physical displays and signal transmitters in the plant. The TCG20 cloud gateway can also further process the data of the DX80 receiver module instead of the HMI. This allows the machine values to be sent to the Turck cloud via the mobile network or via Wifi, optionally hosted also without an Internet connection as a private cloud in the in-house IT center. The TCG20 also supports the connection to other cloud environments in exactly the same way. Benefit: Information can be called up day and night on any connected terminal device such as a smartphone or tablet and linked with alerts via SMS or email. For this maintenance has access to a cloud portal that consists of an individually configurable dashboard.
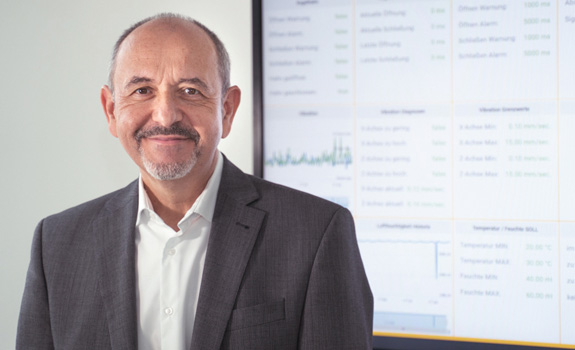
Conclusion
With its condition monitoring solutions, Turck is responding to two frequent problems in the field of maintenance. Status values from machines are often not known at all or do not reach the right recipient at the critical moment. A complete toolbox is now provided for both scenarios – from the robust sensor in the machine environment right through to visualization on the smartphone. The motor monitoring application is a clear example: No laborious adaption is required, especially in existing plants. Companies can retrofit condition monitoring simply and build their own additional control system.
Author | Dr. Bernhard Grimm is director vertical marketing at Turck
Blazing a Trail for Predictive Maintenenance
Maintenance strategies can be divided into three levels. A reactive approach aims to carry out repairs and device replacements only after a malfunction. Preventative action on the other hand means maintenance operations being carried out at fixed times, which are based on empirical values. Condition-based maintenance is based on the evaluation of data from the condition monitoring system together with the real-time diagnostics. Condition monitoring thus provides the fundamental conditions for intelligent forecasts. These provide the basis of predictive maintenance, a core issue of Industry 4.0.
- Topics & Technologies