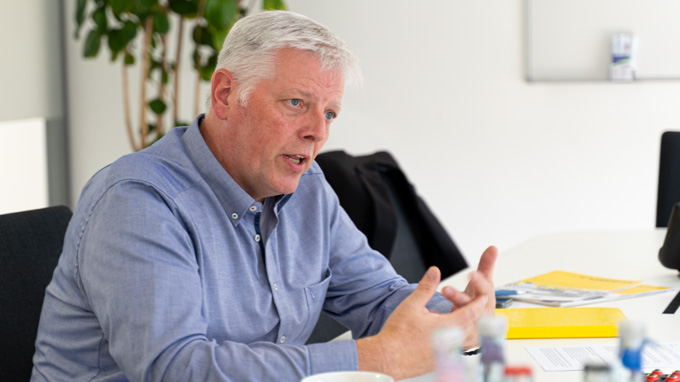
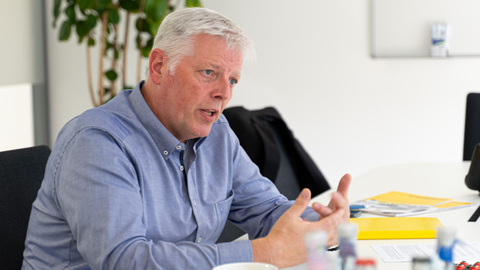
“The Safe Link modules enable the creation of safety solutions without Profisafe or CIP Safety.” – Michael Flesch, Safety Systems Product Manager
Smart IP67 Modules Simplify Machine Safety Applications
Turck sees itself primarily as an automation partner in the field of decentralized IP67 solutions. In this interview with KEM editor in chief Michael Corban, Michael Flesch, safety systems product manager at Turck explains how the portfolio can also implement safety automation tasks. Flesch sees opportunities for the new multiprotocol safety I/O modules with the Turck Safe Link protocol, but also with the use of IO-Link Safety.
What's new at Turck in the field of safety technology?
Michael Flesch: At the SPS in Nuremberg, we presented our TBEN-LL-4FDI-4FDO safe multiprotocol I/O modules with the safe Turck Safe Link protocol. The modules can communicate safely with each other and use the user's existing network structure to do so. Like the non-safety multiprotocol modules, they work automatically in one of the three protocols Profinet, Ethernet-IP or Modbus TCP. The Turck Safe Link modules can reach each other via the Safe Link protocol and thus exchange data safely. They do not require any ongoing control or communication. CIP Safety via Ethernet IP or PROFIsafe are not required for this.
How important do you consider the IO-Link standard for safety technology? Do you support IO-Link safety?
IO-Link Safety in my view is probably the best way to reliably implement more complex applications. These can be very easily integrated into the respective fieldbus systems via the masters. There is currently only one implementation for PN/PS, CIP-Safe via Ethernet/IP and FSoE are in preparation. I assume we will be able to integrate IO-Link Safety quickly into our sensors. There are currently many analog safety tasks, such as pressure, temperature or flow monitoring, which can only be implemented in safety machine applications with a great deal of effort. IO-Link Safety will simplify many applications here.
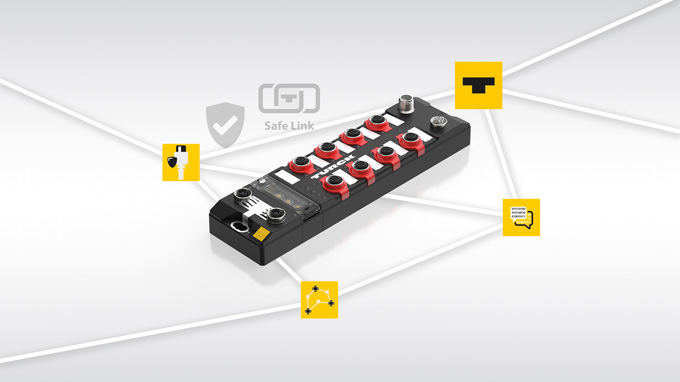
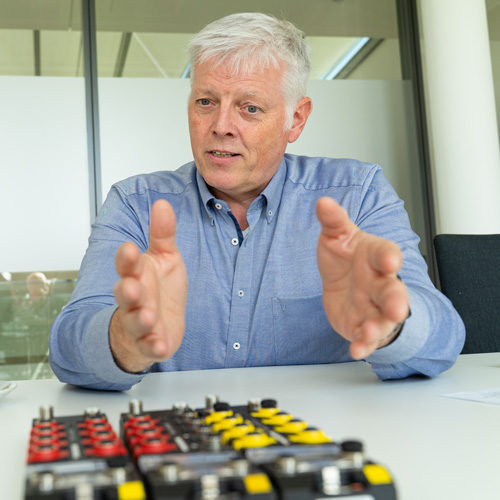
How is Turck's safety technology integrated into the engineering systems of the fieldbuses and Ethernet protocols?
For this we provide our TSC configuration software, the “Turck Safety Configurator”. This allows the modules to be configured at the inputs and outputs in order to obtain the safety CRCs for the engineering system. This is required for both the TBPN and TBIP modules. To make it as easy as possible for customers, basic configurations are offered that provide a basic program directly based on the hardware settings of the modules. This configuration is then simply loaded into the module. The modules can then be integrated into a safety PLC. iPAR and SSID are then communicated to the customer via a validated protocol. The software also makes it possible to link the inputs and outputs in the module directly with each other in order to deliver the result to a safety control system. This enables faster shutdowns than via the link to the PLC and back again. As a result, our modules are able to work safely without FS-PLC, thus allowing a new, modular approach to customer applications.
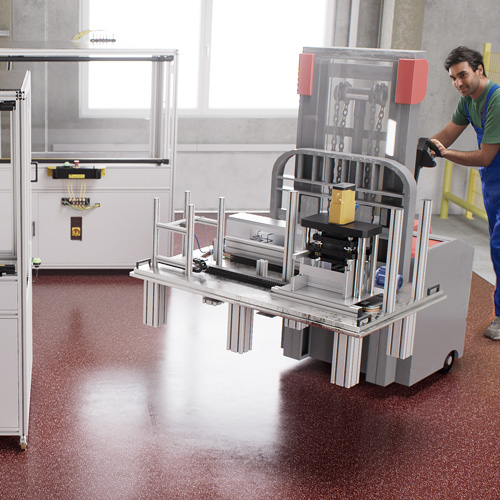
This is an interesting feature – Turck's control technology is primarily based on
the decentralized modules of the TBEN series. To what extent can safety control systems also be implemented?
Our TBEN modules are provided with galvanic isolation of the two voltages V1 and V2 in one string. This allows us to safely switch off the V2 voltage for the outputs via IP67 rated TBSB switch boxes. The user can thus use a fault exclusion for the non-safety output modules in order to be able to execute the calculation to verify safety more easily. We offer as assistance a VDMA database for all safety modules, which can be integrated in Sistema, but also in other calculation tools. Together with the safety portfolio of our optical sensor partner Banner Engineering, we can offer our customers a complete solution for machine safety, apart from safety actuators.
Expert Talk: Turck Safe Link
Walk & Talk: Turck Safe Link
Which IP67 safety components do you offer for machine and plant engineering?
Our IP67 safety components are divided into two different families: The devices with Ethernet/IP and CIP safety communication on the one hand and ProfiNet/ProfiSafe communication on the other. Both series consist of two module series, the half-full or hybrid safety modules and the full safety modules. The first group features a safety and non-safety side. Two IO-Link master ports and two further non-safety I/O connections, the DXP ports, are provided on the non-safety side. The two DXP ports can be safely switched off internally. The second IO-Link port also features a complete safety shutdown function. This allows group shutdowns of downstream outputs in the hybrid module, which is a very attractive feature for some applications.
The individual modules have different voltage connections: a 5 or 4-pin 7/8" connection or an M12-L coded connection for higher currents. The maximum total module current is 9 A, a 2 A supply per port is possible up to this total current. This makes it possible to even switch large actuators such as valves directly.
By the way: All modules can also be used as a reliable safety relay in IP67, which makes the use of a failsafe control unit in conjunction with a non-safety control unit unnecessary in small applications. A combination of both is also possible, i.e. decentralized in the field, with safety communication for failsafe control. This can lead to faster shutdowns, which may be important in some applications. This is only possible as these are modules that are configured or parameterized via the Turck Safety Configurator. The GUI is already optimized for use with a control unit, so that you can reach your goal quickly and easily.
To what extent are safety functions mapped in Turck's cloud concept?
Profinet/Profisafe and Ethernet IP CIP Safety cannot be integrated directly into a cloud solution. This only works via the controller – and even then, it is not secure! However, our new, safe multiprotocol I/O modules can be accessed directly from the cloud via Modbus TCP, just like the standard I/O modules. This allows diagnostics, approvals, and status to be transferred. However, none of this is functionally safe.
Author | Michael Corban is editor-in-chief of the trade journal KEM Konstruktion | Automation
- Topics & Technologies