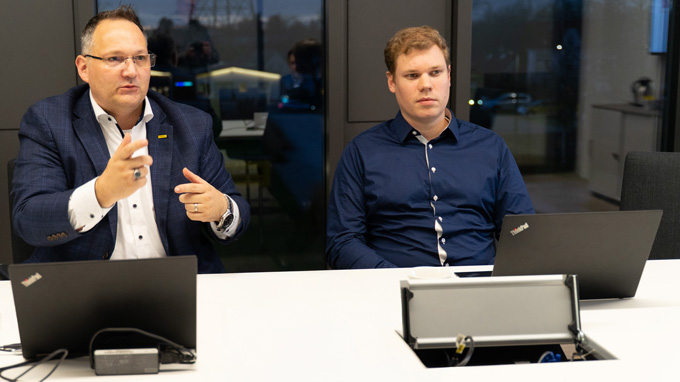
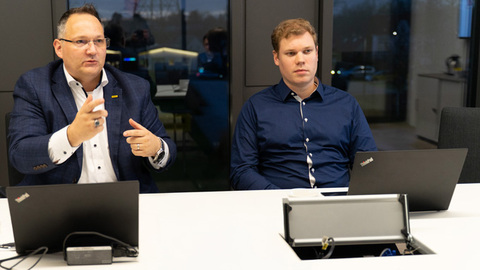
Dezentrale Steuerungstechnik für modulare und skalierbare Förderstrecken
Mit kompakten I/O-Modulen seiner TBEN-Reihe kann Turck nicht nur Trommelmotoren in Rollenbahnen ansteuern, sondern gleichzeitig die ganze Förderstrecke digitalisieren und für Transparenz in der Intralogistik sorgen. Im Gespräch mit den vier Turck-Spezialisten Frank Morassi, Holger Spies, Frederik Nitsche und Hendrik Schnabel erfuhr Michael Corban, Chefredakteur der Fachzeitschrift KEM Konstruktion | Automation, wie dezentrale Automatisierung, Modularisierung und Digitalisierung flexibel skalierbare und hochverfügbare Förderstrecken ermöglichen – besonders effizient in Kombination mit RFID-Technik zur Identifikation des Förderguts.
Welche Herausforderungen adressiert Turck mit seinem Angebot für die Intralogistik?
Frank Morassi (Vertical Sales Manager Intralogistics): In der Intralogistik gleicht keine Anlage der anderen – gefragt ist vor allem Flexibilität. Einerseits bezüglich der eingesetzten Komponenten, andererseits aber auch mit Blick auf den schnellen Umbau der Förderanlage, wenn sich wie heute die Anforderungen oft und schnell ändern. Auf Seiten des Maschinenbaus lautet die Antwort darauf Modularisierung, in der Automation ist es die dezentrale Automatisierung in Verbindung mit der Digitalisierung – und hier kennen wir uns aus. Auf diese Weise lassen sich modulare, flexibel skalierbare Förderstrecken realisieren – die bei Bedarf zudem hochverfügbar sind und staudrucklos arbeiten. Mit diesem Ansatz können wir eine Reihe von Aufgaben lösen, die sich in den kommenden Jahren verstärkt stellen.
Ändern sich die Anforderungen, ist neben dem schnellen Umbau einer Anlage zusätzlich Skalierbarkeit gefragt. Modular aufgebaut und dezentral automatisiert, lassen sich Fördermodule schnell und einfach entsprechend einem neuen Streckenlayout umstellen und ergänzen. Mit smarten und robusten I/O-Modulen „an Bord“ bleibt der Verdrahtungsaufwand gering – zudem bringen die Module Steuerungsfähigkeiten sowie Anschlüsse für Aktoren und Sensoren inklusive 24- oder 48-Volt-Spannungsversorgung gleich mit. Da wir mit unserem Angebot schon immer modular und ganzheitlich denken, kann Turck Intralogistikspezialisten eine Lösung aus einer Hand bieten – und bringen dabei dezentrale Automatisierung, Traceability, Condition Monitoring, Scalability, eine schnelle Time-to-Market und digitale Services mit unserer Turck Automation Suite TAS zusammen. Nicht unerwähnt bleiben soll an dieser Stelle zudem unser langjähriges RFID-Know-how.
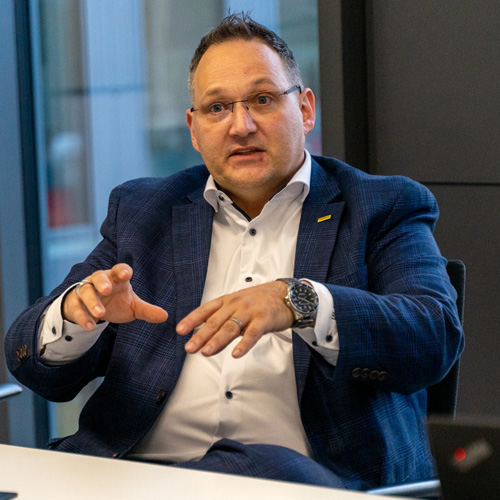
Wollen Sie das etwas näher erläutern?
Morassi: Bei der Vielzahl von Aufgaben – da wird beispielsweise etwas zusammengebaut, geschweißt, gelötet, verpackt, eingelagert, zwischengelagert, umgelagert oder umgepackt – gilt es, genau zu erfassen, welche Box oder Baugruppe sich zu einem bestimmten Zeitpunkt an welcher Stelle befindet. Das können wir mittels RFID gut erfassen – und zwar nicht nur über Gates am Warenein- oder -ausgang. Wir können an den jeweiligen Stationen Ein- und Ausbuchungen im übergeordneten System veranlassen. Ein enorm wichtiger Vorteil von RFID ist dabei, dass ich den Datenträger im Gegensatz zum Barcode nicht nur lesen, sondern auch beschreiben kann. So lassen sich zum Beispiel bei Montagevorgängen die Seriennummern der verbauten Teile und Baugruppen einfach mitgeben – die Nachverfolgbarkeit ist sichergestellt.
Sie sprachen auch das Thema einer schnellen Time-to-Market an...
Morassi: ...weil das einer der Vorteile der dezentralen Automatisierung ist. Wir können eine Anlage deutlich schneller realisieren, weil dezentrale Anlagen autonom laufen und geprüft werden können. Eine neue Anlage oder auch eine Anlagenerweiterung sind damit schneller implementiert. Parallel haben wir die Möglichkeit, Daten sehr einfach zu gewinnen und zu verarbeiten. Damit lassen sich Mehrwerte generieren – etwa bei Service-aufgaben, nicht zuletzt auch über die Datenauswertung in der Cloud.
Hier kommt unsere Automatisierungssoftware ins Spiel, die Turck Automation Suite TAS. Mit diesem Tool können wir alle Komponenten mühelos einbinden und integrieren. Idealerweise ist dazu jedes Element einer Förderstrecke mit einem unserer I/O-Module ausgestattet – sodass Daten aufgenommen und an die übergeordnete Steuerung weitergegeben werden können.
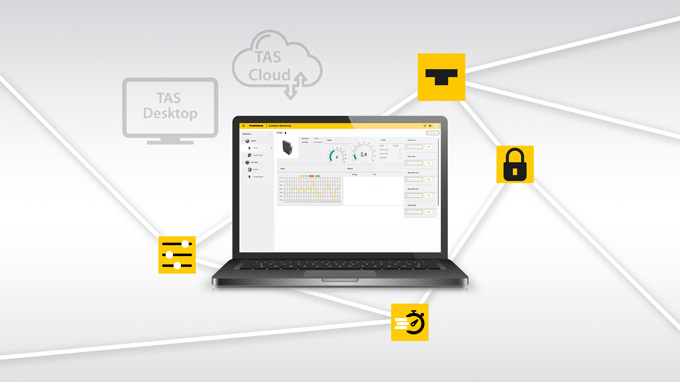
Ihre smarten I/O-Module bringen ja auch eine Steuerung mit – wie spielen lokale und übergeordnete Steuerung zusammen?
Holger Spies (Projektmanagement Vertrieb): Indem wir ‚an jedem Meter‘ der Förderstrecke eines unserer TBEN-Module verbauen, ermöglichen wir nicht nur die volle Kontrolle der Rollenmotoren in dem jeweiligen Fördermodul, sondern wir können auch alles, was sich lokal – sprich dezentral – steuern lässt, über die integrierte Steuerung ansprechen. Hervorheben möchte ich, dass wir sogar Aufgaben mit Echtzeitanforderungen abarbeiten können. Die übergeordnete Steuerung muss dann keine Detailaufgaben auf den einzelnen Modulen übernehmen und orchestriert nur die Gesamtanlage. Neben die Steueraufgaben der Module tritt dann zusätzlich das Erfassen und Weitergeben von Daten für die vorausschauende Wartung (Predictive Maintenance).
Lassen Sie mich das kurz an einem Beispiel klar machen: Nehmen wir an, ein Paket soll an Station X ausgeschleust werden. Dann erfassen wir die Informationen vor Ort und geben sie über unser Modul weiter – will heißen: Wir identifizieren das Paket und steuern über die dezentrale Automatisierung vor Ort die entsprechende Ausschleuseinheit. In gleicher Weise trifft das auch dann zu, wenn es sich um eine Real-Time-Anwendung handelt. Über die zentrale Steuerung müssen in diesen Fällen keine Informationen laufen. So lassen sich beispielsweise die Motorrollen dezentral vor Ort entsprechend der jeweiligen Aufgabenstellung bewegen.
Mittels des CAN-basierten Kommunikationsprotokolls können wir dabei parallel weitere Daten übermitteln und bestimmte Profile fahren oder umgekehrt Werte für Temperatur, Strom und Spannung auslesen. Ziel ist, eine digitale Durchgängigkeit zu erreichen und auf diese Weise die Limitierungen der üblicherweise genutzten analogen Schnittstellen aufzuheben. Die Digitalisierung gibt uns so die Möglichkeit, die Transparenz über den Zustand der ganzen Anlage zu erhalten – bis in den letzten Meter hinein.
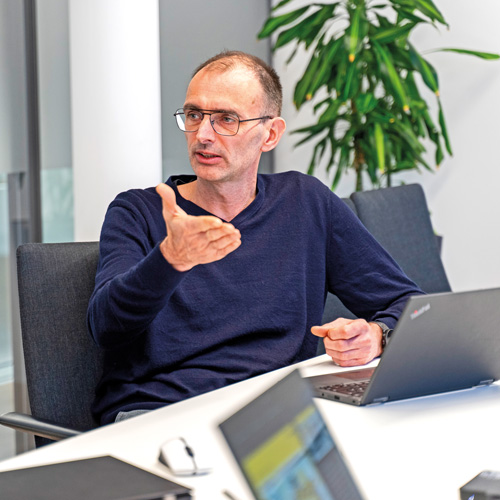
Das ermöglicht dann das Condition Monitoring?
Spies: Exakt! Denn jetzt können wir auf die einzelne Motorrolle heruntergebrochen angeben, wie viel Strom sie benötigt – was einerseits mehr Steuermöglichkeiten eröffnet, andererseits aber auch die Grundlage für Predictive Maintenance legt. Erst mit dieser Datendurchlässigkeit kann der Anlagenbauer seinem Kunden beispielsweise anbieten, bestimmte Motorrollen vorausschauend zu wechseln – wenn sie etwa nach einer definierten Betriebsstundenzahl anfangen, höhere Ströme zu ziehen.
Zusammenfassend lässt sich sagen: Mit der dezentralen Automatisierung können wir insbesondere auch Real-Time-Anwendungen dezentral vor Ort abarbeiten und so volle Flexibilität von der Steuerung über die Skalierung von Förderstrecken bis hin zu Lösungen für Predictive Maintenance bieten.
Was zeichnet die zum Einsatz kommenden smarten I/O-Module noch aus?
Frederik Nitsche (Produktmanager Fabrikautomation Systeme): Wir bauen unsere IP67-Module grundsätzlich für harsche Umgebungsbedingungen – speziell in der Intralogistik ist hier die Vibrationsfestigkeit gefragt. Darüber hinaus erlauben wir auf der Motorversorgungsebene auch eine Spannung von 48 Volt – das klingt trivial, halbiert aber effektiv die Ströme, was gerade in ausgedehnten Anlagen der Intralogistik nicht unwichtig ist.
Jedes Turck-Modul kann vier Rollenmotoren versorgen und steuern – und damit ein komplettes Fördermodul. Wie schon erwähnt, sind wir bezüglich der Steueraufgaben dabei natürlich nicht nur auf die Rollenmotoren beschränkt, sondern können auch weitere Aufgaben erledigen. In der Summe steht dem Intralogistiker so eine leicht und flexibel einsetzbare dezentrale Logik zur Verfügung, die auf den Fördermodulen sehr effizient arbeitet und auch die staudrucklose Förderung ermöglicht. Auf diese Weise lassen sich wunderbar Segmente von Rollenförderanlagen automatisieren.
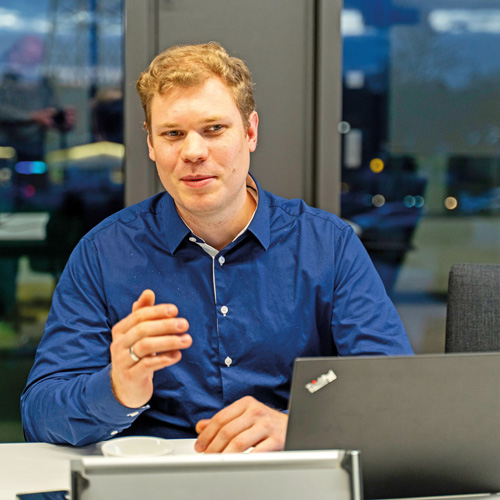
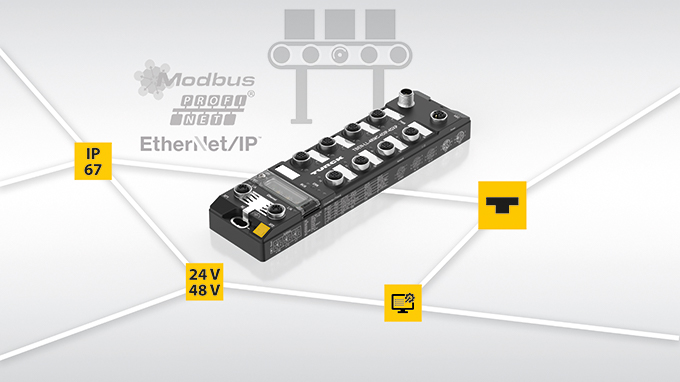
Bin ich bei den Motorrollen auf bestimmte Hersteller angewiesen?
Nitsche: Aktuell unterstützen wir die CAN-basierten Motoren von MTA, MPC und Interroll. Entsprechend dem Kerngedanken der Modularisierung kapseln wir sowohl die eigentliche Logik als auch die digitale Rollenanbindung – auf diese Weise muss sich niemand mit dem Thema Daten-Mapping plagen und man kann jederzeit wahlweise über Profinet oder EtherNet/IP die Geschwindigkeit steuern oder umgekehrt Daten für Predictive Maintenance auslesen.
Basierend auf unserem I/O-Modul TBEN-LL4RM-4DI-4DXP haben wir beispielsweise für SSI SCHÄFER ein Modul zur „Conveyor Control Unit“ weiterentwickelt. Neben der 48-Volt-Spannung für die Rollenmotoren und 24 Volt für klassische Aktoren, CAN-Kommunikation zum Motor und Profinet-Kommunikation zur Steuerung waren hier digitale Ein- und Ausgänge für externe Trigger-Signale oder Aktoren eine weitere Anforderung. Zusätzlich zu vier klassischen I/Os stehen auf dem Modul vier DXP-Ports bereit, die vom Anwender wahlweise als Ein- oder Ausgang genutzt werden können.
Spies: Wie gesagt lassen sich mit diesen Modulen auch Echtzeit-Steuerungsaufgaben lösen, vor allem im Zusammenspiel mit Turcks RFID-System – etwa unserem neuen UHF-RFID-Tunnel. Häufig habe ich in der Intralogistik Aufgabenstellungen der Art, dass ich etwa prüfen will, ob in einer Box auch wirklich fünf Datenträger enthalten sind – sind nur vier drin, muss ich die Box direkt ausschleusen und zurückfahren können. Wichtig ist, dass der Anwender immer entscheiden kann, ob er solche Aufgaben dezentral auf dem entsprechenden Modul oder zentral lösen will – wir können beides. Das ist vor allem auch bei Erweiterungen und Umbauten ein sehr großer Vorteil.
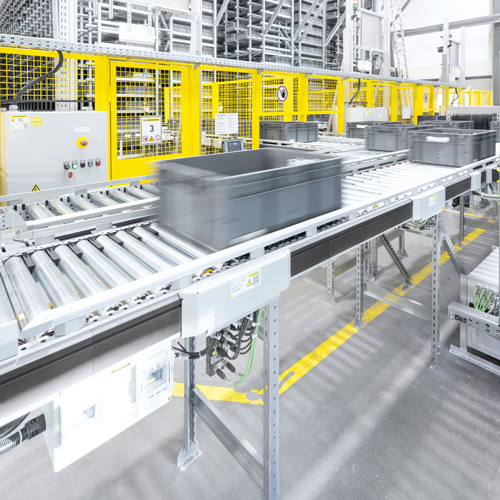
Wie leicht lässt sich denn solch ein RFID-Tunnel integrieren?
Hendrik Schnabel (Produktmanager RFID-UHF-Systeme): Sehr leicht – und vor allem skalierbar. Unser RFID-Tunnel liefert einen RFID-Lesepunkt, der sich sehr einfach auf die Fördertechnik aufsetzen lässt. Ich betone das deshalb, weil die Realisierung solch eines Lesepunkts im Umfeld der metallenen Fördertechnik nicht trivial ist. Um reproduzierbare Ergebnisse zu erhalten, muss die Lesestelle gut geschirmt und auf das Förderband ausgerichtet sein. All dies ist bei unserem RFID-Tunnel bereits gegeben – was den Vorteil bietet, dass der Anwender bei einer Anlagenerweiterung leicht weitere Tunnel ergänzen kann – alles ist bereits vorkonfektioniert. RFID spielt an dieser Stelle auch deshalb eine wichtige Rolle, weil wir bei den hohen Anforderungen der Intralogistik an die Identifikation technologisch an eine Grenze stoßen, an der Barcodes nicht mehr ausreichen.
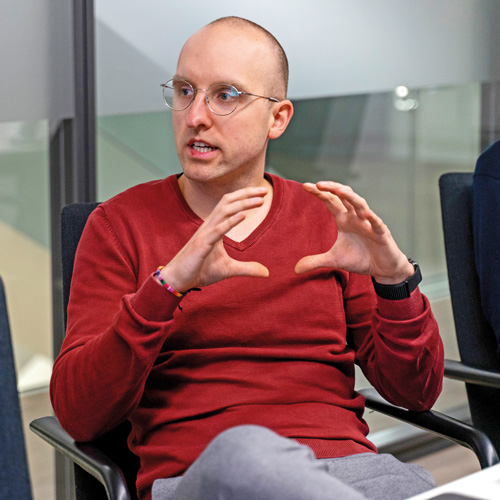
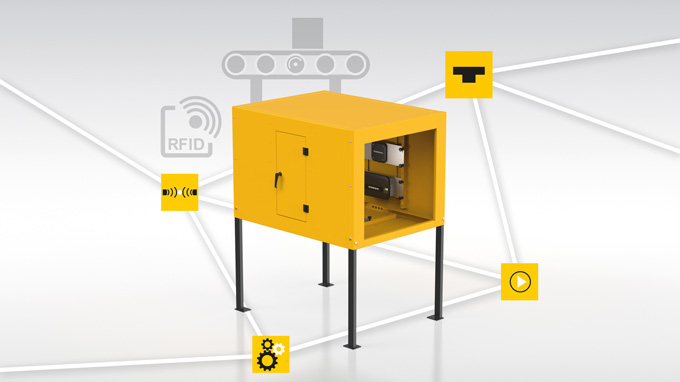
Sie sprachen das metallene Umfeld bereits an – ist das Lesen von RFID-Tags auf Metall oder Flüssigkeiten gelöst?
Schnabel: Das ist grundsätzlich noch immer ein Thema – aber eine Lösung existiert beispielsweise in Form von speziellen Metalldatenträgern. Sollten solche Anforderungen vorhanden sein, bieten wir zusätzlich auch Beratungsleistungen an – denn diese Fälle sind meist komplex und erfordern ein genaues Hinschauen. Im Wesentlichen werden allerdings in der Intralogistik heute Kunststoffbehälter und -träger eingesetzt, so dass das Lesen der Tags problemlos ist.
Autor | Michael Corban ist Chefredakteur der Fachzeitschrift KEM Konstruktion | Automation
Weitere Informationen
- Themen & Technologien